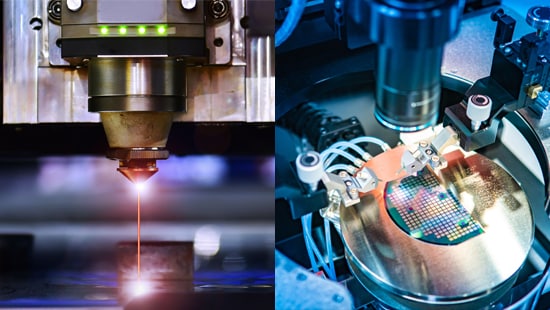
Water Treatment for Process-Critical Closed Loops
Maximize the operational efficiency of your process-critical systems with our safe, efficient, easy-to-use solution for these integrated closed loops.
Our offerings for process-critical closed loops (PCCL) help you properly control temperature, increasing equipment throughput and efficiency while reducing downtime and total cost of operation (TCO).
What are Process-Critical Closed Loops (PCCL)?
- PCCL are systems, typically with small volumes of water (e.g., 5-600 litres), used to cool key processes
- Although the water volumes are small, their role is vital in regulating the temperature of these pieces of equipment
- Without proper temperature control, PCCL processes can’t function effectively. In some cases, the systems must be shutdown or can only operate at reduced throughput and efficiency, increasing total cost of operation (TCO)
Equipment with PCCL may have some or all of the following characteristics:
- Performs a precise job
- Made for high performance and high reliability
- Has a relatively low tolerance for temperature variation
- Generates heat that must be dissipated for the equipment to work properly
Examples of equipment with PCCL include: metal 3D printers, MRI (magnetic resonance imaging) machines, laser cutting tools, semiconductor tools & testers, and supercomputers, among others.

Laser Cutting Tools

MRI Machines

Metal 3D Printers
Learn More About Water Treatment
for Process-Critical Closed Loops

Brochure
Learn more about process-critical closed loops

Enhancing Productivity in the Microelectronics Industry
A semiconductor producer and a testing equipment manufacturer saved more than $700 million per year with a program for process-critical closed loops from Nalco Water.
Why is proper treatment critical for these loops?
Four water-related problems are most common in these types of systems:
- Scale
- Microbiological growth
- Corrosion
- Fouling
These issues can result in reduced efficiency, increased downtime risk and loss of production throughput. When poor water treatment quality is the issue, customer or production personnel dissatisfaction can occur with the equipment. This can lead to diminished equipment sales or additional warranty-related support costs.
Products such as deionized (DI) water, ethylene glycol and glycol-based additives are commonly used to dissipate heat in PCCL equipment. However, assessments show traditional options may not successfully mitigate all four potential issues. The Nalco Water PCCL program efficiently addresses all of these water-related problems, while achieving optimal heating transferring capacity.

Without effective water treatment

After implementing a water treatment program from Nalco Water
Nalco Water Approaches PCCLs with Your Success in Mind
Nalco Water works with you and your design engineers to examine existing and potential designs. Often, water-related challenges can be avoided with careful consideration in this phase.
Nalco Water works with you at your manufacturing site, ensuring PCCLs are kept free and clear from microbio fouling, scale and corrosion as they’re built, avoiding in-transit water-related issues.
Once certified for shipment, our Build Clean protocols provide you and your customer with confidence that the unit is ready for installation and start-up when it reaches its final destination.
The treatment protocol developed by you and your Nalco Water team will be designed to maximize uptime, provide for environmental and regulatory compliance and ease of end-customer application.
How does Nalco Water support PCCL Systems?

Consulting Analytical Support
- To determine causes of water-related challenges your customers may be experiencing
- Solutions might be metallurgical, treatment, operational or a combination

Training
- For your service and field engineers, so they can convey the impact of these programs to your customers
- Develop case studies with you to accentuate the competitive advantage your products can offer when paired with a Nalco Water program
- Properly deploy and implement water treatment programs

Customized Treatment
- Customized treatment chemistry for your PCCL systems
How can you show a return on your investment
with Nalco Water?

We can work with you to measure improved customer satisfaction, reductions in downtime and/or warranty claims and improvement in results. Potential areas of return include:
- Reduced risk of customer production losses due to insufficient cooling
- Reduced risk of production curtailment or quality loss
- Higher customer satisfaction due to higher system uptime
- Enhanced reputation for reliability
- New, recurring revenue and profit streams from treated water solution sales